
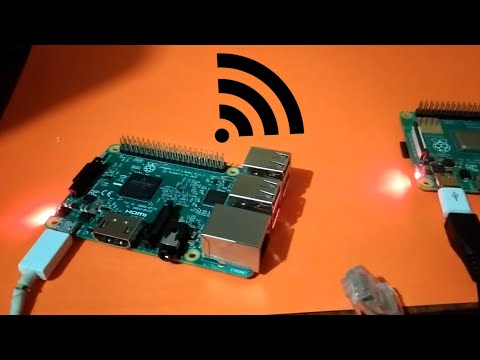


The third dimension, Θ (theta), is then achieved by rotating the object to a new slice. In radial coordinates, this picture would yield both the r and z components. In image processing, the distance between each segment of the line from the center of the object could be collected. This projection could be captured on the Pi Camera (PiCam), have its perspective corrected, and then filtered prior to image processing. The central component in this design is the line laser that projects upon a vertical slice of the objects. With our background in computer graphics, embedded systems and mechanical design, we decided that this was a feasible and interesting project for our team to take on. The cost of these scanners is often quite expensive. The ability to quickly scan existing objects can make them easy to reproduce, and facilitates designing other parts around them. The inspiration for this project came from our past experience with 3D printing and rapid prototyping.
Repetier server raspberry pi conect outsidde full#
The object is spun on a rotating tray, and the process is repeated until the full object is scanned. The camera detects the slice’s distance from the center to give a mesh slice. The laser is positioned 45 degrees askew from the laser, and projects a bright red line on one vertical slice of the object. The device does this by utilizing a line laser and the Pi Camera to perform computer vision. obj mesh files for reproduction using 3D printing. Our Laser Scanner project is a Raspberry Pi-based embedded system device that’s able to digitize objects into.
